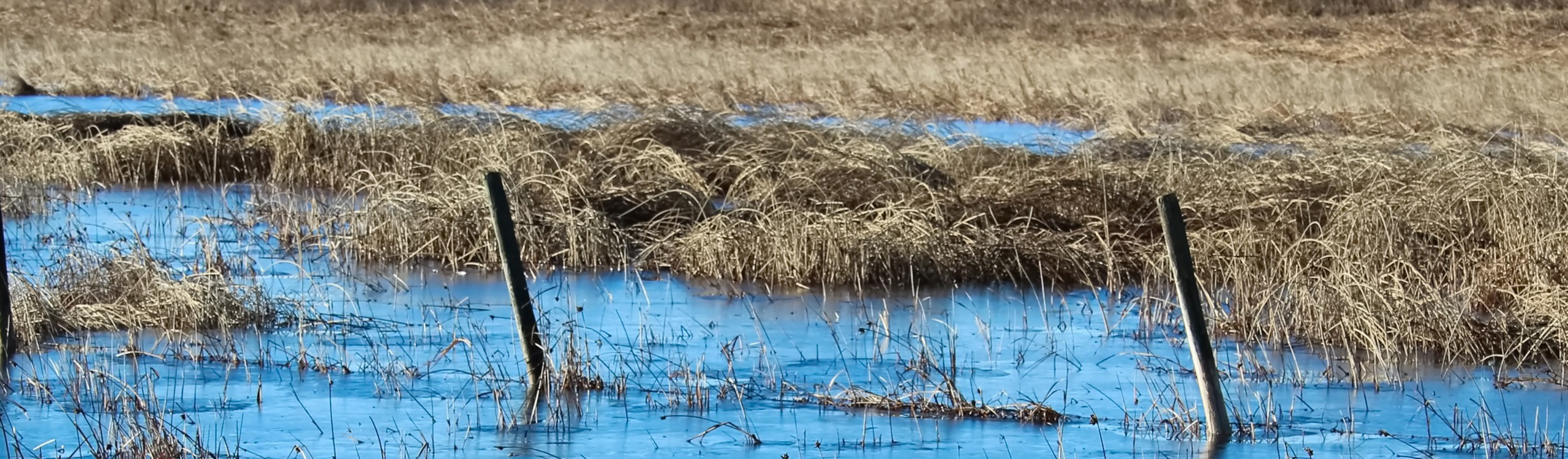
Asset Management Technology
Asset management technology involves systems that leverage interconnected software and hardware,enabling people and organizations to obtain real-time data and monitor information regarding how infrastructure is managed, the conditions of infrastructure and/or assets, and the performance of management practices. Two such systems are Supervisory Control and Data Acquisition (SCADA) and Internet of Things (IoT) systems.
SCADA is a computer network that gathers and analyzes real-time data regarding the workings of an infrastructure system, and then monitors and controls any equipment that might be remotely controlled. IoT is a network of computing devices (e.g., smartphones) connecting people/workers and physical objects (e.g., a valve) using the internet. Using sensor and wireless technologies, physical “things” can identify themselves to computing devices, emit real-time data, and be controlled in pre-programmed or manual ways. In some IoT systems, an object can function smartly, by combining its feedback information with that from other sensors and devices, and the entire system can help make more informed decisions about operations and maintenance (O&M).
Both SCADA and IoT can perform real-time remote monitoring, analytics, and control functions, and have major advantages in terms of helping to make faster and smarter decisions and save money by applying real-time data analytics. However, most SCADA systems are proprietary and isolated within one utility (improving its security), whereas IoT is ubiquitous, and has many avenues of access and connection (improving its interoperability but weakening its security).
Stormwater O&M functions can be supported by various computer-based technologies, where the need for real-time monitoring and real-time control systems might be present. As the traditional SCADA systems advance in terms of their power and security, and as the IoT starts to evolve into a mature set of technologies, several approaches are available to serve two key functions related to stormwater infrastructure: real-time sensors and data collection devices, and real-time control systems.
Supervisory Control and Data Acquisition (SCADA)
Overview
SCADA is a dedicated monitoring and control system that uses computer and communication technologies programmed for specific processes. SCADA systems vary in function and complexity, but they generally provide remotely accessible real-time data information and control functions. These systems are
currently used in, and are essential to, several industries such as manufacturing; water treatment and distribution; and wastewater collection, conveyance, and treatment.
What is it used for?
SCADA systems have proven to be a tremendous asset to infrastructure and facilities management and should be considered as a stormwater management resource based on a jurisdiction’s unique characteristics and needs. A common application for a SCADA system is to send alarms to designated personnel when equipment is malfunctioning or a problem is sensed. SCADA systems are also configured to allow for control of infrastructure components. The capabilities of specific SCADA systems can be simple (sending alarms) or extremely complex (running automatic control protocols based on sensor data). The following are examples of small- and large-scale SCADA systems.
Small, Individual Systems
Small and inexpensive SCADA systems are used on all types of small infrastructure to provide appropriate monitoring and control functions for a given project. Individual SCADA systems are economical and substantially reduce the number of person-hours spent on-site. The Rose Hill Landfill in Narragansett, Rhode Island, uses an individual SCADA system cooperating with a flare unit. The purpose of the flare is to burn excess methane gas produced by the decommissioned and capped landfill. This installation is essential because of the danger associated with the accumulation and migration of methane gas, especially with several residential properties nearby.
A SCADA system was the logical choice for this installation because of its dual functions:
- the system uses sensors to monitor gas flow rate and system functionality
- it has output relays to control blower operation
The SCADA unit resides inside the flare unit, is connected to utility power (with a back-up battery), and is connected to a cellular network for data transmission. The owners and operators of the flare unit access the SCADA data from the system manufacturer’s website portal. In addition, designated personnel are sent notifications via phone calls or text if there is an issue, such as a pump malfunction, to get immediate notice when someone must visit the site for maintenance. This arrangement provides real-time information on unit operation (e.g., by measuring instantaneous gas flow), it also provides historical data and trends, such as how much gas is produced in one week. These data are exportable and manageable in the form of a Microsoft Excel spreadsheet.
Large, Integrated Systems
Larger-scale use of SCADA elsewhere illustrates the extensive potential of such control systems. For example, SCADA could monitor and control much storm protection infrastructure, including multiple pump stations. At each pump station, a SCADA system monitors pumps, engines, water flow data, fuel levels, local weather, site security cameras, and more. The same SCADA system can also control flood gates, providing water level control. Using a SCADA system would enable remote monitoring of system performance particularly during serious events like hurricanes. Building such a system may require hiring several firms to design a complete customized and integrated system. The cost of a more complex SCADA system could be justified by the costs that would be avoided during a major hurricane.
SCADA: How It Works
Regardless of the size or complexity of a Supervisory Control and Data Acquisition (SCADA)
system, each system comprises four main components:
- the supervisory computer (accessed via the Internet in basic systems)
- the remote terminal unit (RTU) and programmable logic controller (PLC) installed at the equipment site
- some means of communication (which may be cellular telephone, an Internet connection, or other means)
- the human-machine interface (HMI)
In smaller systems, these components are integrated into a single package installed at the remote site, and the HMI is a web-based portal. A summary of each component is provided.
Supervisory Computer(s) Remote Terminal Unit (RTUs) and Programmable Logic Controllers (PLCs)
RTUs and PLCs connect to sensors and actuators and are networked to the supervisory computer. RTUs and PLCs may be connected to sensors for recording flow, levels, temperature, voltage and current, or almost any type of measurement. Stormwater applications may include rain or surface water level gages. They may have control relay outputs that perform equipment on/off functions. PLCs and some RTUs can be programmed to perform simple computing for automatic function without input from the supervisory computer.
Communication Infrastructure
This component provides communication between the supervisory computer and the RTUs/PLCs.Communication infrastructure is most commonly by cellular data or by Ethernet/Wi-Fi. A “plain old telephone service” connection or a licensed frequency radio modem may also be used, depending on site-specific requirements.
Human Machine Interface (HMI)
An HMI is an extension of the supervisory computer and the device/software or way the end user receives the data, monitors the system, and/or receives notifications. Commonly, the HMI is a web-based software that is accessed via a computer or phone. HMIs vary in how they display: although some may graphically show the system operating, in most cases, the HMI presents reports, shows system status, and sends alarms and notifications. In basic SCADA systems, the HMI is simply a cell phone that is sent a text or call when the system is malfunctioning or another issue occurs.
SCADA Implementation
Implementing Supervisory Control and Data Acquisition (SCADA) systems into infrastructure is useful for several applications. Some examples of process monitoring and control include:
- Real-time data monitoring (e.g., flow, level, temperature, pressure, rainfall)
- Remote control of pumps, motors, valves, gates, etc.
- Monitoring and/or controlling in locations that are remote or difficult to access
- Situations where early problem detection results in major risk prevention
- Controlling equipment in time-sensitive systems
- Automation of performance to optimize results and minimize costs
Cost and Installation
Like most investments, the long-term value of incorporating SCADA into operations must be weighed against initial and ongoing costs. The capital and life-cycle costs of a SCADA system vary with the type and size of the system that is installed, as well as the third-party services that it may require. Fortunately, the benefits of SCADA are used economically in smaller applications.
Single-unit SCADA monitors, such as the one at the Rose Hill Landfill, may be installed by utility staff and are priced in the $1,000 range with an approximate $300 annual cost to the service provider. Large, integrated systems could cost in the hundreds of thousands to millions of dollars when considering the customized design, hardware, installation, and configuration. In addition, these large systems often require significant operating costs to hire information technology (IT) consultants or employees to constantly maintain the system, server, and its security.
Training
Training may be required before operating and navigating the human-machine interface (HMI). For large SCADA systems and plant operations, the operator must be experienced with use of the HMI and the industrial process. However, because SCADA systems are used to make processes easier and because the technology has improved over time, most HMIs are user-friendly and easy to learn. Providers of package SCADA systems provide free comprehensive training, live support, and responsive callback for after-hour emergencies. Overall training requirements should not be a major consideration for owning a SCADA system. Accessing and operating most web-based SCADA systems is intuitive to anyone familiar with using the internet. Data are displayed in plain language, for example: “Pump 1 flow: 1,200 gallons per minute (gpm).”
Maintenance
System hardware requires typical maintenance and annual inspections to ensure continued functionality. Typical hardware maintenance could include yearly replacement of backup batteries or infrequent replacement of components exposed to the elements. In most situations, the SCADA system provides notifications of hardware malfunctions.
There is typically no required maintenance for system software and computer hardware, except in cases in which the operator is also the direct owner of the computer and servers. In most cases, (especially in small, individual systems) the provider of the web-based HMI ensures continued operation of the computer, network, and servers, and this service is included in the annual fee. Providers even offer free or discounted upgrades to existing hardware when newer technologies become available.
Compatibility and Adding to Existing SCADA Systems
Municipalities seldom have the opportunity to purchase and install all SCADA components for a system at once. However, with SCADA, municipalities can add new SCADA capabilities as new infrastructure is installed, or as funding becomes available. It is even possible to develop direct data links between two separate systems, which is especially useful when incorporating a new technology such as a SCADA system while maintaining centralized management.
SCADA Stormwater Applications
Supervisory Control and Data Acquisition (SCADA) systems facilitate the gathering and analyzing of real time data, and then the monitoring and control of equipment, such as stormwater facility control, where there are operational and adjustable parts in the facility design. SCADA also can give warnings by sounding alarms if situations develop into hazardous scenarios, such as flooding.
SCADA systems can help with stormwater management by tracking stormwater facility performance using modeling and monitoring feedback, and then by turning on/off system motors, pumps, gates, etc. (as relevant) to provide full operational control. It also provides information about the performance of green and gray infrastructure to inform adaptive design and management for stormwater system improvement.
Data collection systems in SCADA help to identify costs to achieve the human health and welfare and water quality objectives, and the effectiveness of such controls. SCADA also helps in tracking costs and savings achieved due to sustainable design.
Click a topic below to learn more
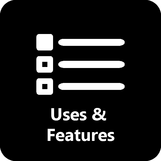
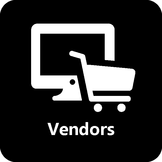

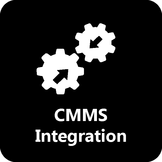
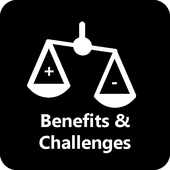
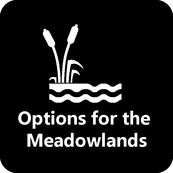
Supervisory Control and Data Acquisition (SCADA) solutions are customizable and may easily include stormwater infrastructure needs. Manufacturers offer white papers highlighting specific stormwater projects and describing how SCADA systems can be integrated into stormwater infrastructure.
Real-Time Monitoring
SCADA is used to monitor elements of stormwater infrastructure and related applications. Obtaining real-time data is crucial in preparing for floods and preventing spills. Also, SCADA can be used to record historical trends, such as analyzing historical wet-weather events, finding problem areas, and designing new infrastructure. Potential uses of SCADA monitoring in stormwater applications include:
- Manhole monitoring for surcharge and overflow
- Flow rates in stormwater infrastructure
- Tank level monitoring
- Rainfall monitoring
- Water levels and/or flow rates in surface waters
- Remotely monitor and log changing water characteristics such as total suspended solids, conductivity, and pH
Remote and Automated Control
Remote control of stormwater infrastructure is essential when quick changes must be made during a storm event. Automated control of structures has the same results and improves operational efficiency. Using SCADA for remote and automated control for stormwater infrastructure may include the following:
- Pump station operation
- Control of gates, dams, weirs, and all types of hydraulic devices
- Disinfection, screening, and other pollution prevention measures
- Controlling traffic control barriers at high-water events
External Equipment
“Bare” SCADA systems, as purchased, provide only signal inputs and outputs. External devices are required to provide useful data inputs. Nearly all the instrumentation used in potable, storm, and wastewater industries provide scalable outputs that may be directly connected to a SCADA system without the need for additional signal conditioning. Examples include magnetic flow meters, area-velocity flow meters, pH/conductivity/oxidation reduction potential (ORP) instruments, and open-contact alarms. Outputs from SCADA often require an external relay to operated high current loads, such
as motors.
Flow and level measuring equipment are typically required in stormwater projects. These instruments are robustly constructed and intended for use in storm- and waste-water environments. When properly installed, they may be expected to have a 20-year service life. Water chemistry instruments, such as pH and conductivity probes, are also robust, but the wetted probes of these instruments have a service life of one to two years before replacement is required. Simple float switches for level control application are durable and inexpensive to replace.
When considering the purchase of any particular SCADA system, it is important to specify the correct number and type of inputs and outputs required to accomplish the desired equipment functions.
Compatibility and Adding to Existing SCADA Systems
Municipalities seldom have the opportunity to purchase and install all SCADA components for a system at once. However, with SCADA, municipalities can add new SCADA capabilities as new infrastructure is installed, or as funding becomes available. It is even possible to develop direct data links between two separate systems, which is especially useful when incorporating a new technology such as a SCADA system while maintaining centralized management.
SCADA System Vendors
Provider | Product | |
Industrial Control Links, Inc. | Scadaworks™ | Visit website |
Mission Communications | M800™ | Visit website |
Phoenix Contact | SMS Relay™ | Visit website |
RACO | Verbatim™ | Visit website |
Wonderware | inTouch™ | Visit website |
The displayed table lists example companies that provide relatively low-cost and scalable web-based Supervisory Control and Data Acquisition (SCADA) systems suitable for installation and use by small- and medium-size stormwater utilities. Other vendors exist in this marketplace and should also be explored. A summary of one company’s products follows this table illustrate the kinds of information that are typically available, and both the list and following discussion are for example only. There is no endorsement intended of any listed or unlisted company or product, and the suitability of any manufacturer or equipment for any installation is the sole determination of the purchaser.
Mission Communications® offers single-source SCADA system products and solutions that have been used for stormwater infrastructure. The company provides users remote terminal units (RTUs), which are set up on-site and configured for the specific requirements and communicate via cellular data transmission. Typically, users take advantage of the Mission web portal for data and reports are accessible from desktops, smartphones, and tablets, an
arrangement that is much less expensive then owning data storage hardware and maintaining networks. However, Mission Communications also offers the ability to integrate data delivery into existing human-machine interface (HMI) software if needed.
Listed below are two of the company’s products that could be useful in a stormwater context:
- Manhole monitor sends notifications via phone, email, text message, fax, or pager when a manhole reaches high levels, using floats as a detection mechanism. It runs on a replaceable battery that lasts years at a time. It provides early surcharge detection and records date, time, and duration of event.
- M800 is a multifunctional RTU that gathers real-time data and controls system components automatically or manually. The unit provides customizable input options used to collect and store data on pump status, flow rate, tank levels, and more. It monitors outside conditions, such as rainfall or river flows, if packaged with applicable add-ons. Inputs are configured with alarm callouts delivered via phone, email, text, etc. and tailored to specific alarming needs. The all-in-one RTU also includes remote control of appurtenances-such as tanks, gates, and screening/disinfection equipment-which may be configured to operate automatically.
The Mission Communications® website illustrates potential use of its products and a newsletter with examples of specific applications.
Kearny, New Jersey
At the Municipal Sanitary Landfill Authority 1D landfill in Kearny, NJ, the New Jersey Department of Environmental Protection (DEP) uses relatively simple and easily deployed Supervisory Control and Data Acquisition (SCADA) equipment. During construction, SCADA is used to monitor pore water pressure and lateral slope movement of the landfill cap. The system collects readings automatically and wirelessly from inclinometers and piezometers, and it is used for web-based reporting of data from all instruments. This system will be removed at the completion of construction.
A second SCADA installation that will be permanent monitors two leachate pump stations and provides monitoring and limited control functions of the unattended gas extraction and flare system. Data collected includes wet-well level, pump fail conditions, volume of leachate conveyed to sanitary sewer, volume of landfill gas extracted, and gas flare operating parameters and alarm conditions. This data is conveyed by cellular telephone modem to a web-based monitoring and alarm system. This system is expected to remain in operation indefinitely.
Pawtucket, Rhode Island
In Pawtucket, Rhode Island, the Narraganset Bay Authority (NBC) uses a simple SCADA system to monitor and control the first constructed wetland stormwater capture and filtering system installed in the state. This facility is located at a stormwater outfall and captures and retains the first flush of heavily contaminated stormwater. The subsequent flows are diverted to a system of constructed wetlands for treatment and eventual discharge to surface waters.
SCADA is used for flow measuring and characterization (pH and conductivity) of the stormwater. The first flush is always captured, but when the conductivity of the water falls below a set point, a sluice gate is automatically opened, diverting flows to the constructed wetland. The level of the retained flow in a concrete tank is measured, and when capacity exists in a nearby interceptor sewer this stored flow is pumped to a sanitary sewer for treatment. SCADA is also used to measure the level in the bar screen channel both upstream and downstream of the screen. When the differential level across the screen reaches a certain point, an alarm message is sent indicating the screen needs cleaning. The SCADA system also operates a sampler, which recovers grab samples of the water discharged to surface water.
This relatively simple SCADA system allows the facility to operate unattended, yet flows through the facility are monitored and recorded, and alarm conditions are promptly reported, which eliminates the need for a crew to inspect the facility after each flow event. The flow data captured are used for regulatory compliance and modeling of the watershed.
This example project, which has successfully operated for more than 5 years, illustrates the diverse uses SCADA has in stormwater capture and reuse applications. Basic parameters-such as flow, water characteristics, and tank levels-are measured by external instruments connected to the SCADA system. Operational requirements-such as operating gates, valves, and pumps-are either automatically controlled through simple logic, or manually operated via remote control. Alarm messages are sent to maintenance personnel for action. Accurate historical data in a human or machine-readable format is available for regulatory and engineering use.
Some utilities now have some form of Computerized Maintenance Management System (CMMS) or asset management system, which is a computerized system to store information about assets. Typically, geographic information systems (GIS) is integrated.
Supervisory Control and Data Acquisition (SCADA) systems and asset management systems have different purposes: the former for the direct monitoring and control of equipment, and the latter for recording asset data and managing work orders. Depending on the exact functions desired, however, it is possible to integrate some aspects of SCADA (typically, equipment alarm history) into an asset management system.
Asset management systems that are built using open standards, which means they store data in an open, published format using standard commercial Structured Query Language (SQL) databases, such as Oracle and Microsoft SQL Server, are appropriate for integration with SCADA systems. The open standards design of such systems, such as Cityworks, allows the development of custom software that interfaces between a SCADA system and the asset management system. These interfaces may be created in-house or by a third party. While technically feasible, this effort may entail substantial lead time and capital costs. The more complex SCADA systems that have customer-owned and -maintained servers are more amiable to integration with
asset management systems. If less complex, web-based SCADA systems are in use, however, the cost of integration into an asset management system-that is, the custom software development-may exceed the cost of the SCADA system by an order of magnitude.
HydroCAD and StormCAD are both proprietary software, from two different developers, used for the design and analysis of storm sewer systems. Neither is
open-standard software, and it is not possible to integrate data directly into these programs. The software licenses generally prohibit alteration or
reverse-engineering of the software by the licensee. However, historical flow data from a SCADA system may be, and commonly is, used as the basis for design when using either of these programs. As previously mentioned, most SCADA systems export recorded data in Microsoft Excel format. These data may be manually imported into either program. Products from Bentley Systems including WaterCAD (series 5 and later editions) allow SCADA data to be automatically imported into their hydraulic models for use as initial conditions. System operators benefit from the ability to publish model results to the utility’s existing SCADA system control screen, helping forecast operating conditions.
Implementation of Supervisory Control and Data Acquisition (SCADA) across infrastructure would reduce operational and maintenance labor requirements and
allow for rapid response to storm conditions and infrastructure breakdown or failure, which is essential when access is limited or dangerous during storm surge or high stormwater flows. In addition, integration of SCADA into infrastructure components would provide water level and flow data that could be stored and tracked over time. Aggregation of these data would inform jurisdictions as they plan for maintenance and future improvements.
Benefits
Operations
Remote access through SCADA enables operations staff to review alarm conditions and decide if an in-person response is necessary. In some cases, corrective actions can be taken without dispatching staff to the facility, which can result in a significant savings in labor hours.
Regulatory
Routine reporting requires the analysis of water quality parameters that are observed using instrumentation and could be recorded by the SCADA system. Exporting these data in a format suitable for reporting to regulatory authorities with minimal manipulation is an important feature of most SCADA systems.
Engineering
Engineers use the historical data to plan the future needs of the stormwater system. Having usable data at hand can mitigate or eliminate the cost of
flow-metering projects to acquire engineering data.
Troubleshooting mechanical problems
By observing trends of various parameters over a range of time scales, it is often possible to deduce related events that would otherwise be impossible to observe. Considerable savings in labor hours can be realized when diagnosing elusive system problems.
Situational awareness
SCADA allows operations staff to see what is happening in a system in near real-time. Potentially hazardous conditions, such as a rising stream level,
are immediately apparent without the need for direct observation of the site.
Mobility
Nearly every available SCADA system has full functionality available through tablet and smart phone devices, allowing access to essential information while in the field. Accordingly, operations staff are no longer tied to a central desktop computer.
Challenges
Cost
A potential obstacle to implementation is the interconnected nature of the improvements and their reliance upon coordinated operation for maximum efficacy. SCADA would best be implemented on all storm surge protection features simultaneously, to control and monitor the entire system remotely instead of piecemeal. Such a coordinated and integrated SCADA system could entail higher capital costs and design, however, than a smaller or piecemeal system.
Training
The interface chosen-whether provided by the SCADA vendor or in concert with a Computerized Maintenance Management System (CMMS) and asset management system could entail a learning curve for existing staff or require new hires with skills necessary to manage and operate the system. Early wins and quick troubleshooting will be imperative to demonstrate to existing staff that the SCADA system is reliable.
Stormwater projects typically incorporate Supervisory Control and Data Acquisition (SCADA) systems to provide monitoring, control, reporting, and alarm functions. The proposed Meadowlands Rebuild by Design (RBD) infrastructure could incorporate SCADA technologies.
- For the proposed infrastructure to be built by 2022, the new stormwater pumps at East Riser Ditch and Losen Slote Creek could be automatically operated based on water levels and flow rate, and the status of the pumps could be remotely monitored. The quantity and quality of stormwater flows in channels, ditches, and green infrastructure enhancements could trigger diversion to constructed wetlands, traditional stormwater infrastructure, or other downstream bodies and send alerts prompting maintenance of a specific feature.
- SCADA could be integral to additional storm surge protection improvements, if planned for the future.
- Although still under development, Internet of Things (IoT) sensors could be implemented at the proposed green infrastructure or streetscape type improvements and parks. Such implementation would be especially useful as the workforce evolves to incorporate green infrastructure maintenance skill sets.
Internet of Things (IoT)
At present, infrastructure management is evolving to incorporate Internet of Things (IoT) technologies. Recent innovations in small, inexpensive microprocessors (a physically small and inexpensive computer processor operating at low speeds with a limited number of input and output functions but having connectivity via the Internet) has led to IoT. IoT allows “things” to connect and interchange data. An example of an IoT device is a refrigerator that can report its contents to a smartphone app, or the use of a home “smart speaker” to control lighting and climate control systems.
What is it used for?
IoT sensors for environmental applications may be based on small, inexpensive microprocessor boards, such as the Arduino or Raspberry Pi (these two products are functionally identical and both are in the $20 range). External sensors for parameters such as flow, rainfall, and temperature are added to the basic microprocessor board. An additional stacked Ethernet board provides for data transfer to a remote computer.
IoT: How It Works
To operate, Internet of Things (IoT) devices require loading of firmware[1], much of which has already been developed and is publicly available online. If desired, custom firmware also may be developed using the popular C/C++ language. A suitable enclosure must also be provided. Power requirements for these sensor packages are so low they may be provided by batteries or small photovoltaic panels.
These projects commonly use Arduino-based sensors because of their flexibility, ease of programming, and cost-effectiveness, and the Arduino platform has become a de facto standard for environmental application simply because of cost and a wide availability of sensor options. In terms of communication and data acquisition, an Internet service provider (ISP) provides communication with the Arduino-based sensors, and Google Charts has been used for data visualization. This framework for sensor data monitoring allows for seamless integration of all types of sensor data across a common platform for users to easily share the data.
Implementing such a network of environmental sensors requires only a modest amount of technical knowledge; similar projects are often undertaken by high school students. Hardware cost per deployed sensor package is in the $100 range (price is approximate in 2019 dollars and subject to change).
Comparison to SCADA
In many ways, IoT behaves as a Supervisory Control and Data Acquisition (SCADA) device. Some have argued that IoT represents the fourth generation of SCADA. However, SCADA is the recommended tool for process control (due to superior security), while IoT is recommended for environmental monitoring.
SCADA is typically configured as a closed, non-internet-based system with a defined system command structure, and thus it often has built-in application-specific security and encryption. It also tends to be focused on real-time system management (e.g., when to open a valve based on pressure)
and less focused on aggregated data collection and data pattern analysis to enhance performance.
SCADA systems for monitoring and control of critical infrastructure are mechanically and electrically robust and intended for permanent installation. Enclosures and electronic components are military-grade, featuring signal isolation (typically up to up to 4 kilovolts), extended temperature operation (-40°C to 85°C), high retention electrical and data connectors, and industrial steel enclosures for shock and vibration mitigation. They may be expected to have a 20-year or greater service life.
In contrast, although IoT microprocessors are able to control equipment, IoT is not an advisable approach for control of any sensitive or mission-critical component. The open-source operating and communication systems of these devices is inherently insecure. The possibility exists for even a
relatively unsophisticated unauthorized person to interfere with the operation of critical equipment.
Arduino-based sensors are inexpensive and appropriate for non-mission critical applications, especially when the sensor package may be lost, damaged, or vandalized. Hardware costs are low enough that they may be considered as expendable items.
[1] Firmware is a small piece of software that serves a narrow purpose. It is embedded in a piece of electronic hardware to allow operability.
IoT Stormwater Applications
Green Infrastructure Use
Green infrastructure projects generate quantities of environmental monitoring data from variety of sensors. These data are valuable for all related research areas, such as air quality, air pressure, chemical absorption rates, humidity levels, water levels (flooding), soil moisture content, sunlight, precipitation, and temperature. To be usable, these data must be subject to data sharing and analysis on a common platform. The ideal operating environment should efficiently capture data from various sensors, store them in a database, and have a user interface for data retrieval.
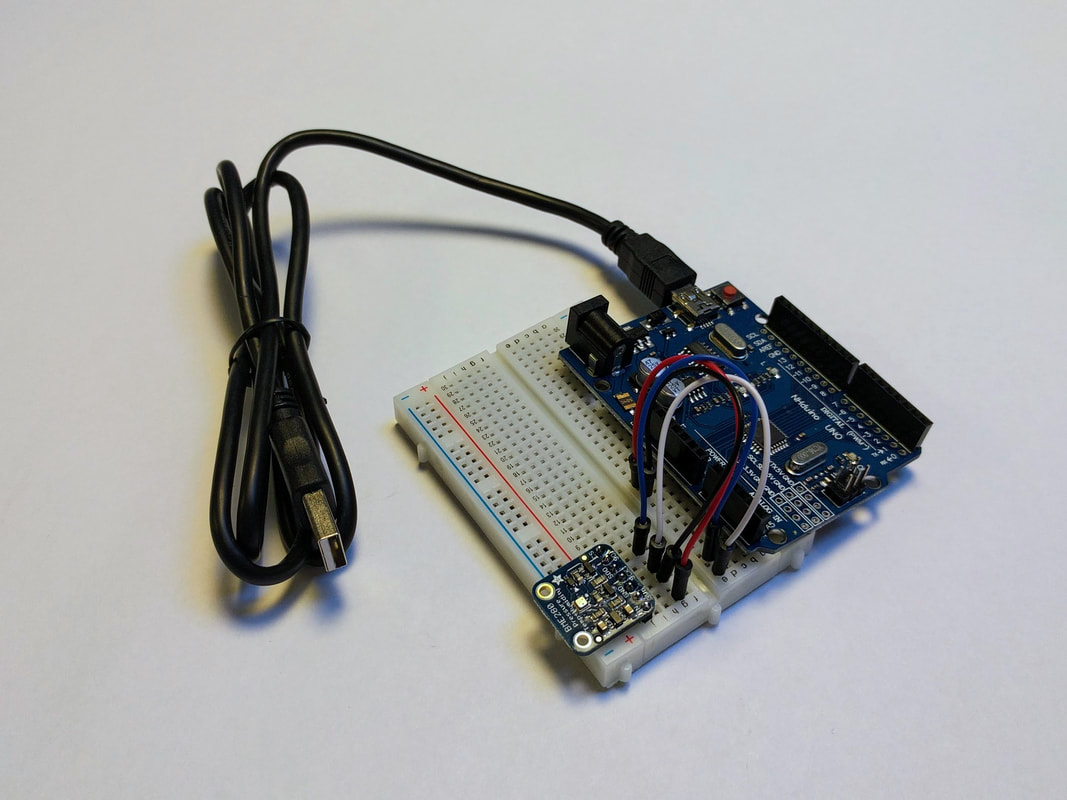
Example Projects
The Nevada Solar Energy-Water-Environment Nexus Project comprises hundreds of inexpensive Arduino-based sensor packages recording solar power, temperature, and wind speed/direction deployed over a large geographic area. Sensor data are collected and stored in a common database that is accessible to scientists and engineers in a wide variety of disciplines. Designing the sensor package around the inexpensive Arduino microprocessor has reduced the cost of each deployed sensor from $50 to $1,500. The same strategy could be employed using any environmental sensor, such as stream or rainfall gages.
Under a pilot project, the Philadelphia Water Department (PWD) installed Vegetronix VH400 capacitance probes in bioswales. When moisture content drops below a specific threshold, the probe can trigger automatic irrigation, or it can send a signal to a maintenance crew that watering is required. Data on soil moisture content are collected and sent to a cloud-based storage solution, where it can be analyzed and downloaded to other platforms.
In a partnership with greenSTEM, PWD also experimented with solar birdhouses in schoolyard gardens. The birdhouses have two rooms-one for birds and one for electronics. Temperature and soil moisture readings indicate when school gardens require watering, and the birdhouse conditions and activities are monitored by sensors and an infrared camera. The entire apparatus can be built for $80. More information is available at the greenSTEM web site. PWD implemented a similar apparatus, branded as the “Solar Sunflower” in partnership with Code for America.
In Chicago, City Digital-a consortium of entities in University of Illinois (UI) Labs-is undertaking the Smart Green Infrastructure Monitoring (SGIM) pilot project to address stormwater management. At locations at Argyle Street, Langley Avenue, and UI Labs on Goose Island, sensors collect runoff data, which are stored in the Cloud to inform stormwater management planning. The sites are testing grounds for a grand plan to build a network of sensors that will serve as a tool for stormwater management.
This page was informed by these resources.